Contractors typically lean upon established industry norms to calculate their expectations for a typical hour’s labor, or productivity rate, but some in the Gulf South are becoming increasingly concerned that the output side of the equation is in decline. While most agree that the tightening of the labor market and a corresponding decline in the proportion of experienced craftsmen are the primary culprits, others suggest more long-term causes are at play—including an aging workforce, a different generational work ethic and a greater, albeit necessary, emphasis on safety protocols.
In its May report, Construction Productivity in an Imbalanced Labor Market, Construction Industry Resources LLC showed a clear correlation between the decline in productivity and the shortage of essential skilled craft labor, asserting that an imbalanced labor market is a clear leading indicator of poor productivity. In the report, 79% of companies reported that their productivity had not improved or had actually dropped by more than 10%, primarily due to the tight skills market.
While project delays in certain regions have granted a temporary reprieve to the labor crisis in Louisiana, some worry productivity declines will intensify as projects ramp up with an improving oil and gas market. Therefore, many who work in and for the petrochemical industry are looking for answers.
Earlier this summer, an industry panel at the 2016 Petrochemical Engineering and Construction Conference in New Orleans pointed to labor shortages, lackluster labor productivity and high labor costs as serious impediments to future investment and profitability among Gulf Coast owners. In particular, an increase in the number of “traveling” skilled laborers chasing higher wages, they say, has led to a decline in productivity.
Panel member Dan Spinks, vice president and general manager of Fluor Corp. in Houston, said there has been a noticeable decline in productivity across the industry, compounded by rising rates of turnovers and absenteeism. As one solution, his engineering-procurement-construction company has turned to moving work off-site to lessen the burden of managing sizeable workforces. “Productivity is not getting better from what I’ve seen,” Spinks says. “We’ve got some work to do there, in order to improve.”
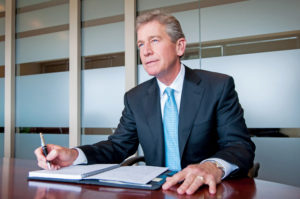
While productivity issues have been especially severe along southeast Texas’ industrial corridor, due to a convergence of sizeable projects there, Louisiana is experiencing its own regional workforce strains. The most immediate concern is in Lake Charles, the site of the state’s largest industrial project—the $8.9 billion Sasol ethane cracker and derivatives plant.
Kim Cusimano, Sasol North America public affairs director, says she expects challenges finding necessary, qualified labor as other projects in the area break ground. “With the number of projects expected to kick off in southwest Louisiana (an estimated $90 billion-plus), we expect there to be significant competition for the local workforce and businesses,” Cusimano says. Much of the impact will likely be felt by Sasol’s 5,000-worker construction force, since the plant’s permanent positions are already 70% filled (350 of 500).
Lee Jenkins, vice president at Performance Contractors in Baton Rouge, which is currently working at the Sasol project, has a “high level of confidence” that his company will be able to man the work there with seasoned, skilled laborers, with the help of the company’s new training facility in Lake Charles. Performance also targets jobs that “make the most sense for us to execute. It’s the type of work, it’s the location, but it’s also the timing, so we can transition employees from one job to the next.”
Jenkins says unprecedented employment is having an indisputable impact upon productivity. “The industry work horse is larger than it has ever been, and there’s no doubt that productivity has been impacted where the megaprojects have affected the workforce the most,” he adds. “When you see multiple megaprojects in close proximity in that area, there’s no question that the construction workforce is impacted by that.”
Fred McManus, chief operating officer for Brown & Root in Baton Rouge, says it could have been worse. Had all of the work projected for 2016 and 2017 actually come to fruition, “we would really be in a tough spot, because there’d not be enough people to do the work. As contractors come closer to maximizing the available workforce, the abilities of the craft that you’re hiring go down.”
FUNCTIONS OF OUTPUT
Jonathan Shi, endowed chair in industrial construction at LSU, teaches a class in productivity and says current productivity woes are simply a matter of supply and demand. Some members of Shi’s class hold upper management positions in some of Louisiana’s largest industrial construction firms.
“When you have more demand and the labor supply is about the same, you have problems,” Shi says. “Most of the shortage is in the highly skilled category—they want someone who has at least five or even 10 years’ experience. And someone who just went through the training process does not have that kind of experience.”
Another function of output is the industry’s aging workforce. In the next 10 years, it is estimated that 30% of the construction workforce will be over 60 years of age. While some say an infusion of younger workers will likely bring its own productivity problems, due to a poor work ethic among millennials, that opinion is not shared by all. Performance’s Jenkins says he thinks it’s less “generational” and more a function of “newness.”
“I haven’t really seen that millennials are nonproductive,” he says. “I think good employees are good employees and they’re productive when they’re well-trained and prepared to do the job that’s out there. I think the key to being successful is minimizing newness on jobs, and when you are dependent upon a large percentage of your workforce coming in as new employees, you’re going to be affected in all areas.”
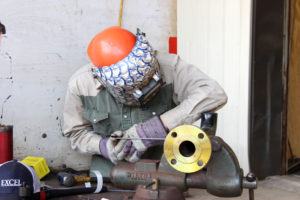
Jenkins points to a convergence of megaprojects in eastern Texas as an example, where productivity has declined due to unprecedented worker demand.
“When you look at what’s going on around Mont Belvieu (Texas), these are monster jobs with huge amounts of people on them,” he adds. “If you go out and have to bring in hundreds or maybe even thousands of people to man a job, and 70% of them are people that have never worked for your company, productivity is going to be affected.”
Brown & Root’s McManus says the increased emphasis on jobsite safety can’t be ruled out as another factor. “Some of these calculations have been based upon the fact that we all have a higher level of expectation for good safety performance,” McManus adds. “We are taking a portion of a person’s day and then we want them to dedicate more time to planning the activities.” He stresses, however, that there is “definitely a return on that investment” in regards to safety protocols.
IMPACT TO THE BOTTOM LINE
When estimating projects, contractors typically adjust their “productivity multiplier” based upon the available crew’s level of experience. If manpower availability is low, the amount of work expected per man hour is adjusted upward.
“If we know the site manager, the superintendent and have confidence in the team of people, we’re going to more aggressively estimate production,” Brown & Root’s McManus says. “Conversely, if we realize we’re only going to know 25, 30 or 40% of that workforce we’re going to add to that factor.” In some situations, Brown & Root has used a “hybrid contract” with its clients, which sets a target price for labor and thereby accounts for the risk in estimating labor cost. In such an arrangement, Brown & Root is penalized when labor cost exceeds the projected amount and earns a bonus if it falls below.
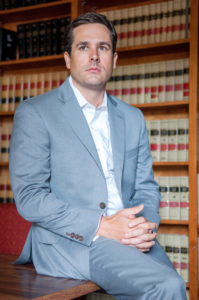
Jay Montalbano, a financial planner with Hannis T. Bourgeois CPA in Baton Rouge and former president of the Construction Financial Management Association’s South Central Chapter, says productivity declines, regardless of the reason, will have a detrimental impact on profitability. His firm specializes in accounting for construction firms.
“It definitely impacts how these guys are estimating their profits,” Montalbano says. “When these clients come calling for a major renovation or new construction, they look internally to see what kind of staff they have and how productive is this staff. That’s going to affect how much the job cost will be.”
Montalbano says rising wages have further increased the squeeze on profit margins, as contractors fight for the same pool of workers. This has also led to the growth of the migrating workforce, or “travelers,” as workers move along the Gulf Coast searching for a higher wage rate. This exacerbates the productivity decline, as these workers must become acclimated to the region and a new plant.
TRAINING, RECRUITMENT AND OTHER SOLUTIONS
Many in the industry are tackling the productivity problem head-on by focusing on the supply side of the equation, primarily through enhanced recruitment and training efforts. In this regard, Sasol in Lake Charles has been impressively proactive in its approach.
“When you are planning to deliver a project the size of ours, it is critical to assess the capacity of the local community, including the local community college and workforce development systems,” Sasol’s Cusimano says. “The Louisiana state community college and workforce systems, particularly McNeese State University, Louisiana State University and Southern University, were among the first we reached out to during site selection. They have a built-in, statewide network of workforce development experts, centers, candidate pools and technology support.”
“We’ve had a number of successes in our workforce preparation efforts due in large part to our partners at the state level and locally,” she adds. “The state invested $20 million into a regional training facility at SOWELA Technical Community College, which will be utilized by Sasol to support its workforce needs for temporary and full-time employees.”
Additionally, Louisiana Economic Development’s FastStart program developed a comprehensive Workforce Solutions Plan to ensure that Sasol has qualified applicants, and the Louisiana Community and Technical College System and SOWELA have been key partners in developing new programs locally for high-demand curriculums.
“Sasol has also partnered with McNeese State University’s Engineering Department for employee training and development courses,” Cusimano says. “In turn, Sasol assists with the McNeese student career planning and professional development programs.”
Sasol provided more than $600,000 in advance funding to the Southwest Louisiana Construction Users Council—tasked with maintaining a steady flow of construction and maintenance workforce—enabling the organization to ramp up training infrastructure and increase accelerated course offerings.
Brown & Root’s McManus says while training has been beefed up at area training centers, the recruitment side of the equation is the greatest challenge. “For most of us in the industry, our fathers, grandfathers and a lot of our relatives were in this business,” he adds. “We grew up with our parents coming home and talking about working a plant, building a refinery, pouring concrete, welding pipe and building forms. We understood that. A lot of the young folks today have no interest in getting into our business. In the end, we’re drafting folks that, on a lot of occasions, don’t have that family heritage.”
An influx of Hispanic workers has also had an impact, he adds. While having a strong work ethic, many require additional skills training to work in area plants.
McManus credits local industry for making significant strides in ramping up training opportunities. “We’re beyond the capacity of the training centers that we’ve developed along the Gulf Coast,” he adds. “Folks such as Baton Rouge Community College and others are starting to realize that there’s a market to provide electrical, welder and carpentry training. We’re taking the expertise that we’ve developed and we’re networking with the educators and bringing them into the craft training world.”
Organizations such as Associated Builders and Contractors have long recognized the importance of recruitment at the high school level, and as such hire former school administrators to lead their training efforts. David Alexander, who served as director of education at ABC Pelican Chapter from January to July, was previously the director of secondary schools in the Ascension Parish school system and principal at Dutchtown High School. (He was hired in late July as the new superintendent of Ascension Parish schools.)
Alexander says recruitment for industrial jobs is difficult because most schools feel that college is the overall objective. “We need to balance the food chain,” Alexander says. “What we have not promoted well is careers in construction. We just haven’t done a good job of that. For me, my role as a high school principal was to get you prepared to go to college. What I should have been doing is getting you prepared to enter the post-secondary world in such a way that you could pursue some specialized skill.”
Alexander says one way to change the college-bound mindset of most faculty could be through six- to eight-week summer “externships,” where teachers get to see the courses they teach in real-world applications.
“That’s when that math teacher goes out and actually sees math and trigonometry in a millwright lab, or when a chemistry teacher actually goes to Dow and sees chemistry in action,” Alexander says. “The problem is there are a lot of high school teachers that have never seen or experienced the subject they teach being used in the workplace.”
MANAGING WITH TECHNOLOGY
Baton Rouge’s Alliance Safety Council leans heavily upon technology to help its members manage current productivity levels, primarily through a records management tool that is gaining widespread popularity.
“The tool helps companies maintain not just an employee’s job history in training but also performs a quick gap analysis,” says Kathy Trahan, Alliance Safety Council president/CEO. “They can quickly query the system to determine how many people they have 100% job ready for a particular site, how many are at 80%, etc. From that, they can prescribe the steps for getting their workers job ready.”
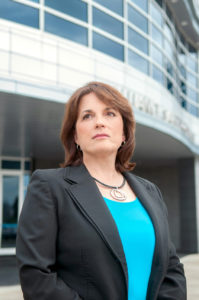
The records management tool provides members with an inventory of current skillsets to determine if additional training is needed when moving an employee from one site to another, or one job function to another.
Hannis T. Bourgeois’ Montalbano has also seen an increase in the use of technology as a productivity management tool. “That can be anything from simply upgrading accounting software to figuring out how to use software to be more productive in the billing cycle, estimating cycle, bid proposal cycle, etc.,” he adds. “There are a lot of programs that are fully integrated; they’ll do it all, from bidding to billing to capturing costs in the field.”
According to panel members at the Petrochemical Engineering & Construction Conference in New Orleans, owners and contractors have drastically increased their reliance on electronic process design and scheduling tools in order to improve efficiency. However, they say controlling capital costs, managing risk and dramatically improving project performance in the current market environment will take more than adopting new technology.
Fluor’s Spinks says his company works to minimize the number of hand-offs and interfaces throughout the lifecycle of a project to drive the certainty and predictability that owners are looking for in their projects. The company is also pushing forward a more integrated and construction-driven approach to its projects that starts as early as the front-end development phase.
To mitigate some of the construction risks, Fluor and other contractors are moving a lot of their engineering and fabrication work offsite, and looking at new modularization approaches and innovations. Spinks says moving the work to a more controlled environment is often more cost-competitive and could drive more efficiency around capital investment projects even as it creates additional project logistics and planning requirements.
While many project owners on the U.S. Gulf Coast are not familiar with modular construction approaches, he said, modularization can significantly offset the impact of falling productivity rates. Additionally, using high-value engineering centers abroad, especially Asia, has become crucial to how Fluor delivers its projects, and the utilization of these offices is increasing as their capabilities continue to rise.
Originally published in the third quarter 2016 edition of 10/12 Industry Report.