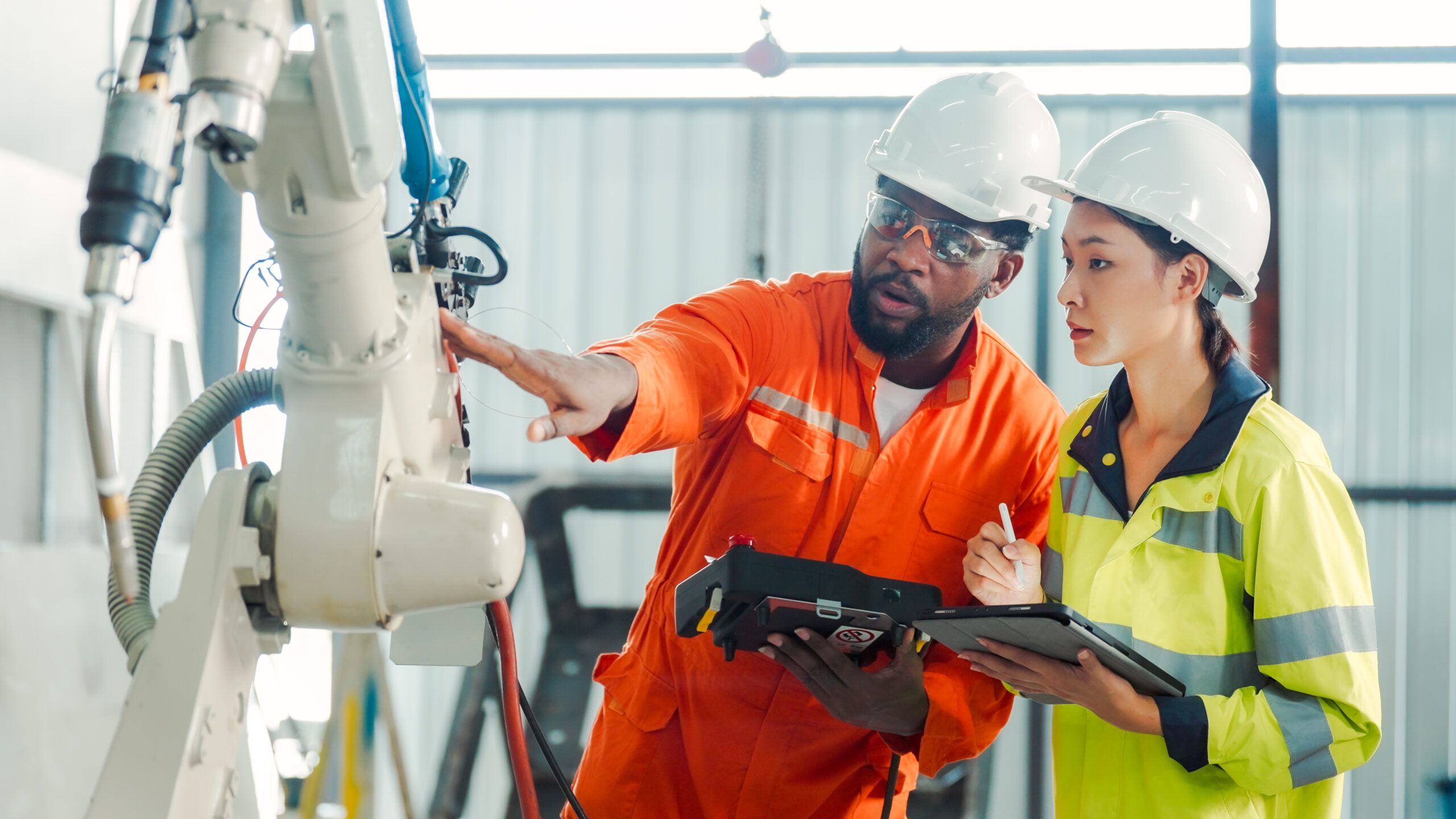
Contractors are engaged in a classic struggle between productivity and prudence as they ramp up manpower in Louisiana’s swiftly growing industrial space.
As they strive to find skilled laborers—and find them quickly—they must also ensure that their new hires are properly trained, screened and oriented to the jobsite.
Various third-party companies that support that effort are speeding up their processes, whether by propping up new brick-and-mortar facilities, nesting at the plants, streamlining procedures or even using AI-supported learning tools that bring the training to the workers.
It’s a challenge that won’t go away anytime soon.
Industrial contractors are expected to face unprecedented workforce needs for years to come, given sizeable investments in new plants and expansions across the state. That will result in a highly competitive labor market.
“Every year we see more patients than the year before,” says Sarah Taylor, owner of Gulf Coast Occupational Medicine in Baton Rouge, a provider of pre-employment and annual screenings. “And every year, we have a bigger staff than the year before. My company runs in direct parallel to the Baton Rouge industrial market. If I’m ramping up, that means Baton Rouge industry is ramping up.”

To shorten turnaround times, Gulf Coast Occupational Medicine operates multiple satellite offices as well as three mobile on-site units. The company plans to open its newest office in Geismar by the end of the year, which will be their 12th location.
“With the amount of traffic on highways 73, 30 and 44 … it gets our services closer to where the people work,” Taylor says. “If someone’s leaving BASF, Shell, etcetera, it will cut 35 to 40 minutes off their commute. That’s a win for them and for us.”
Their mobile units, typically needed for annual screenings or swift ramp-ups in labor, can operate anywhere in the country. While on-site, they can perform a full battery of screenings, including X-rays.
“Our mobile services are aimed at people already at work and on the clock,” she adds. “It’s more efficient for us to come to them. We’re at a site right now for three days testing 260 people.”
UTILIZING AI
Kathy Trahan, president and CEO of Alliance Safety Council in Baton Rouge, is excited about the potential of the council’s AI-enhanced safety orientations, which enables workers to access any course from a computer or smart phone. It’s the latest step in an orchestrated effort by the council to decentralize its operations by bringing the training directly to their clients.
The organization began developing the service for the power industry in 2019 with the help of a Canadian-based tech company.
“We were ready to launch it when COVID hit, so we flipped everything we had to it,” Trahan says. Today, anything in the Alliance Safety Council’s course library can be delivered with the AI component. “It’s super helpful for people coming from out of state who have to be on the job first thing Monday morning,” she adds.
It has become a vital tool in their training portfolio. Last year, the Alliance Safety Council trained more than 240,000 workers in the petrochemical, power, pulp and power sectors through in-person and remote training.
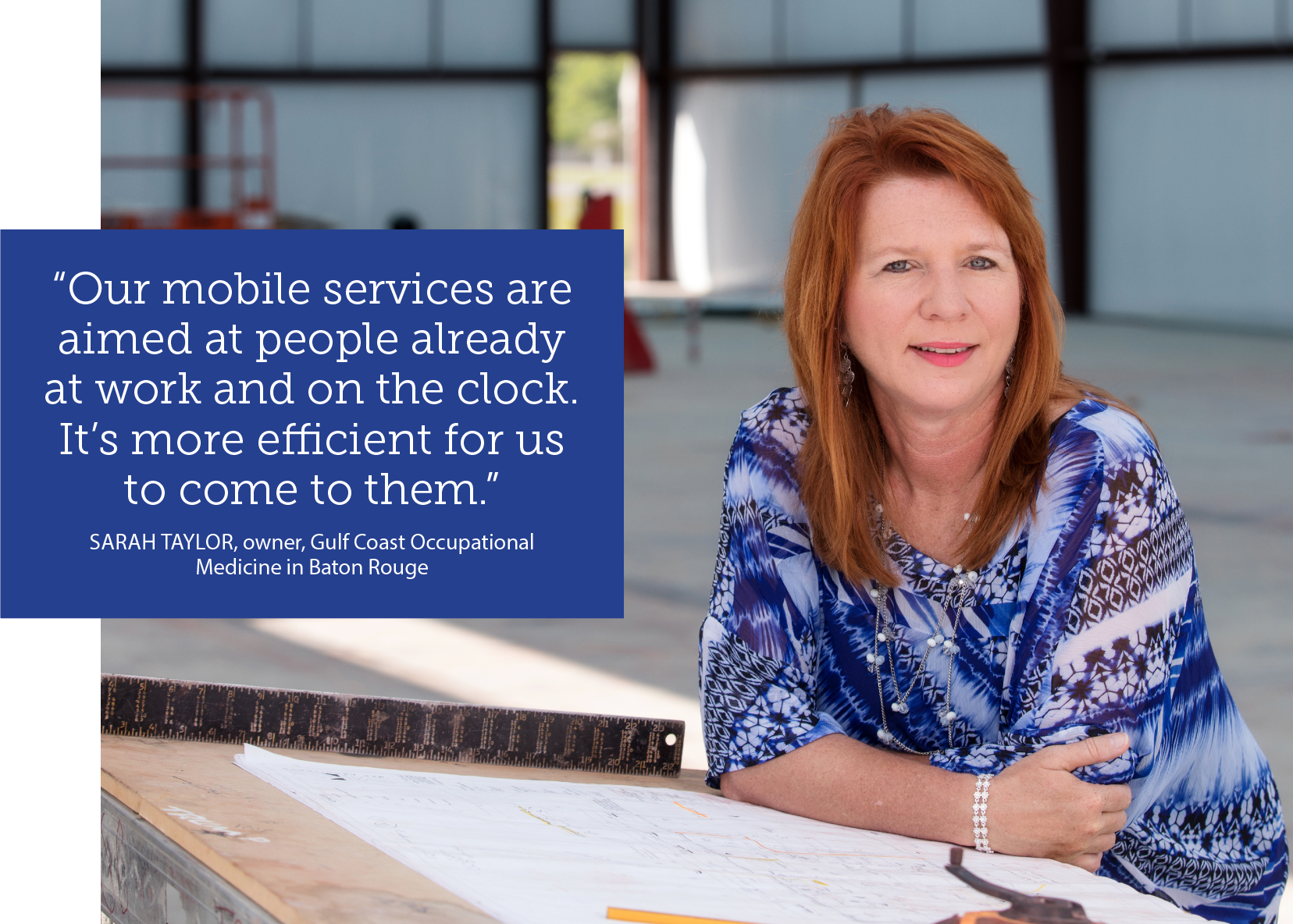
“With the help of AI, we’re now in their pocket; we’re on their phone,” Trahan says. “They can take the training from anywhere with verified proctoring. It allows you to scale quickly, where all these other proctoring systems can be less efficient.”
The AI-supported training tool uses facial recognition and flags anything that might be a testing violation.
“But it can’t do everything, such as determine if an extra set of eyes belongs to a baby or a cat, or someone else who could actually be giving you an answer,” she adds. “AI flags all that, but a human has to verify everything.”
The Alliance Safety Council’s “nesting” services are also growing in popularity. Those provide full-time, five-day-a-week orientation services while physically located at a plant or with a contractor. At present, they’re nested with contractors such as Turner Industries, Cajun Industries and EXCEL Group, and plants such as Dow and ExxonMobil.
The time-saving advantages are obvious, Trahan says. “None of their workers have to travel to our offices; we just integrate into their onboarding process.”
A streamlined approach
For its part, Associated Builders and Contractors’ Pelican Chapter is shortening the length of two of its courses–pipefitting and heavy equipment operation–by eliminating the classroom component in favor of exclusively “hands on” training. That has reduced course times from two years to six months, and significantly improved their ability to get new workers to the field.
By shortening the classes, they hope to achieve the dual goals of improving student retention and increasing graduation rates.
To develop the classes, ABC utilized industrial subject matter experts to ensure they addressed the necessary skillsets. Their first pilot class of pipefitters graduated last summer. “It went well,” president and CEO David Helveston says. “We saw a higher level of engagement from the students. Some of these individuals aren’t book learners and learn best with hands-on training; that’s what they’re going to see in the field every day.”
Student numbers were limited to ensure a small, structured environment for evaluation purposes. “We saw such success and promise that we’re now piloting a hands-on heavy equipment operator class,” he adds. ABC partnered with Louisiana CAT, which provided two simulators and an instructor to work with the students once a month.
The remaining course time is focused on using actual heavy equipment behind the ABC training center. A second pipefitting class is also under way.
The courses will be audited by ABC’s Safety Committee to ensure that safety isn’t compromised in the process. “They’ll perform an audit to identify if we have any shortcomings in our practices,” Helveston says. “It keeps us in check and ensures that we’re providing the latest from industry in regard to safety practices.”
Regardless, safety is embedded in the ABC culture, says Helveston.
“It’s a top priority in everything we do as we teach our classes,” he says. “I think in everything they do and every process there’s a slant on safety and that’s a priority, specifically with ABC and our school.”
Overall, more than 1,000 students are currently enrolled in the fall semester–the highest enrollment for ABC Pelican Chapter since 2020.
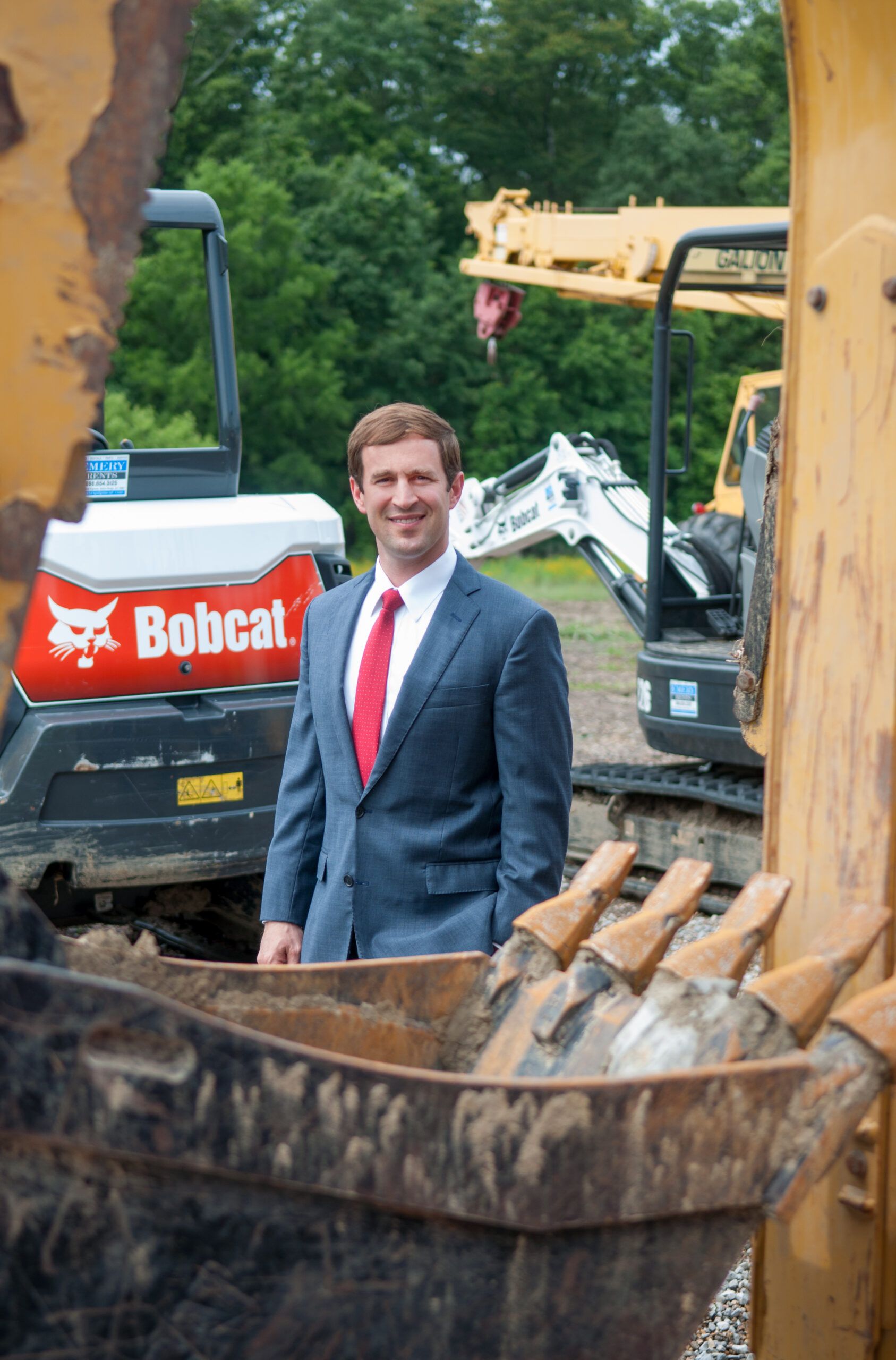
No noticeable cutbacks
Despite the push and pull between safety and the need for speed at the jobsite, Taylor hasn’t noticed any contractors or industrial owners scaling back their screening processes. On the contrary: They’re requesting more comprehensive screenings and in greater frequency.
In particular, she’s noticed a heightened interest in physical abilities testing, necessary to prove that a worker can perform certain tasks such as stepping up and down a ladder and fitting through a small space.
“The pre-employment screening is like Burger King: You can do as little or as much as you want,” she says. “There’s no right or wrong. Of course, the more you do, the bigger impact you can have on the safety of your workforce.
“It’s an ongoing struggle. The safety team wants to screen everyone from their toes to their hair, while operations wants bodies at work to get the work done. Each company has to find its own balance.”