What just years ago seemed like a far-out concept now plays a central role in Louisiana’s manufacturing space. The gathering, manipulation and extrapolation of data via smart facilities, digitization and the Internet of Things (IoT)—aka Industry 4.0—is rapidly gaining a foothold among petrochemical owners.
Some plants are taking a leadership role. Last summer, Cornerstone Chemical in Waggaman kickstarted its efforts by appointing process technology engineer Aubyn Chavez as its first digitization leader. It stemmed from a desire to turn Cornerstone’s Industry 4.0 goals into a sustainable reality.
“Like the old adage, if everybody’s responsible, then nobody’s responsible,” says Tom Yura, chief operating officer. “It became clear that we needed someone with a passion for digitization and a willingness to learn, read and ask questions.”
After assuming the new role, Chavez immediately began taking online classes to understand machine algorithms. She admits to becoming a little obsessed with “PI Asset Framework,” a repository that integrates, contextualizes, refines, references and analyzes data from multiple sources. She even attended the “PI World” conference and talked to people who use the program to collect process data.
“PI AF can support a lot of functions that enable process engineers to make their data work for them,” Chavez says. “It’s great for building out condition-based maintenance for equipment and for building out KPIs (Key Performance Indicators) for processes.”
At Cornerstone, Chavez encourages the adoption and sustainability of digital methods through a mix of education and coaching. “It’s not going to do all the work for you,” she adds. “Instead, it enables the process engineers to become more intimate with their processes and develop some real insights so that we can be more agile.”
Somewhat counterintuitively, Cornerstone implemented its digitization effort from the ground up. Yura says it’s far too easy for companies to roll something out, then let it die on the vine.
“I’d say we have a better chance to be a global leader because we’ve grown the capacity from within,” he adds. “We’ve learned from within, so we can turn this into a fundamental manufacturing concept.”
There was some resistance in the beginning, but Chavez worked closely with engineers to help them understand how digitization tools and connectivity could make their lives easier by providing data-driven solutions. Another obstacle—effectively integrating IT (Information Technology) and OT (Operational Technology) in the same digital space.
In the beginning at least, Cornerstone is targeting two areas—overall equipment effectiveness and raw material consumption. “Are we making the most out of our raw materials onsite? The operations engineers will have real time data and it will allow them to focus on driving production value,” Yura says.
He expects Cornerstone’s equipment uptime to improve and cost of manufacturing to go down as a result.
Outside assistance
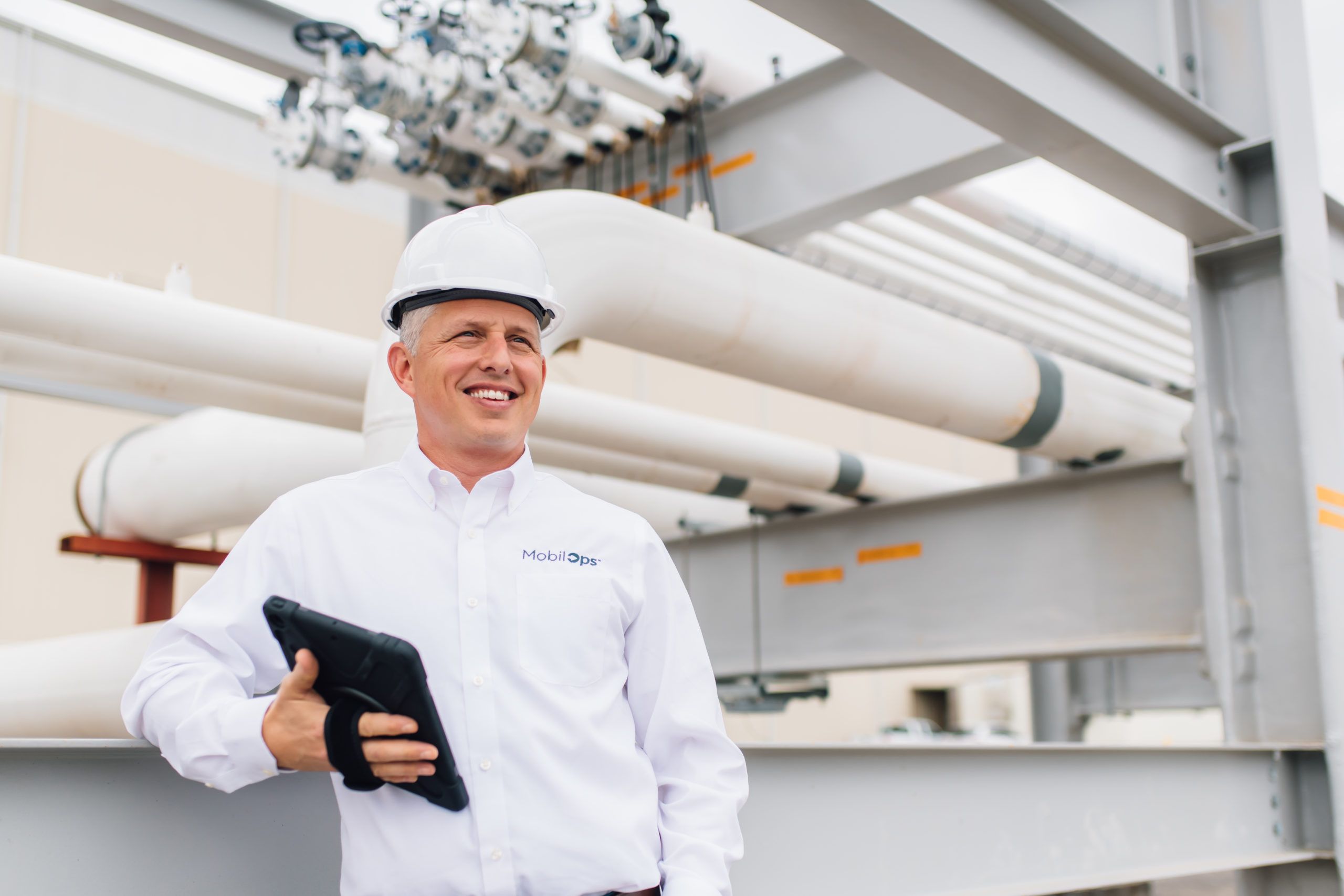
Paul Plauche, director of digital services at Turner Industries in Baton Rouge, says digitization leaders such as Chavez are needed everywhere, as many plants are too decentralized to implement an effective strategy. Turner offers a suite of programs via its MobilOps brand that helps plants manage and use their data.
“I might have a great relationship with the maintenance person and they’ll clearly see where this would be a fit,” says Plauche, who is also general manager at MobilOps. “But then I’ve got to deal with procurement, which is a completely separate organization. Then it’s the plant manager, and then I might get pulled in with a cybersecurity team. And so I have to go through all those different gates.
“If you really want to see movement, there needs to be an overarching embrace by the entire organization, along with clear initiatives. You need to communicate that this is where we’re heading—everybody get on board.”
Turner has had a digital strategy of sorts, for years, with some technologies dating back to the early 1990s. “We’ve won awards for various products to put technology in the field or to digitize our space,” Plauche says. “All the while, we’re staying true to our core competencies of maintenance, construction, turnarounds, etc.”
MobilOps’ suite of programs, which has become increasingly popular as Industry 4.0 concepts gain a foothold, can be packaged with other Turner services. Still, Plauche says outsourcing the digitization process is not everyone’s cup of tea. “Some clients are ‘do it yourselfers,’” he adds. “I know of one company that likes to build all its stuff in-house, yet another who realizes that there’s no way they could do it in-house, given the size and complexity of the process.”
While some plants remain hesitant, the appetite for Industry 4.0 has risen dramatically along the Gulf Coast “due to this phenomenon that’s going on, and everybody seeing the need.” While the adoption of these technologies may seem daunting and a bit risky for some, they’re still taking the plunge in order to remain competitive and viable.
Plauche says digitization can have a direct and significant impact on a company’s ROI. “We always say you can’t run a report from a filing cabinet,” he adds. “If you’re capturing that information digitally, you can do dozens of things with that data.”
Local universities are also offering help. The Industrial Assessment Center at LSU provides free industrial assessments to small and medium-sized manufacturers in the areas of energy efficiency, productivity, sustainability and competitiveness.
Additionally, LSU’s Industrial Innovation Center, funded by the U.S. Economic Development Administration, supports technological advances in chemical manufacturing. LSU is one of 34 organizations providing the service. “Our approach is to work with our industrial partners including plant operators and industrial contractors,” says Jonathan Shi, center director and LSU industrial construction professor. “The LSU-IIC will work with them to identify their technological needs and then match them up with an innovator to develop the technology.”
The LSU-IIC leverages existing industrial partnerships established through the Louisiana Chemical Manufacturing Initiative, or LCMI, which is comprised of more than 90 local partners representing stakeholders from different sectors of Louisiana’s chemical manufacturing industry. It also utilizes and expands the innovation resources available at the LSU Innovation Park and Louisiana Business and Technology Center.
“When information is digital and is structured, it can be searched and analyzed and then used to give the project manager useful information,” Shi says.
According to the professor, Gulf Coast companies might be a bit slow to adopt new things, but he’s noticed a sizeable shift toward digitization and Industry 4.0 in recent months and years. “More people are talking about those kind of things because we are getting more and more globalized,” he adds. “It is important to educate the public and the community about this kind of new technology.”
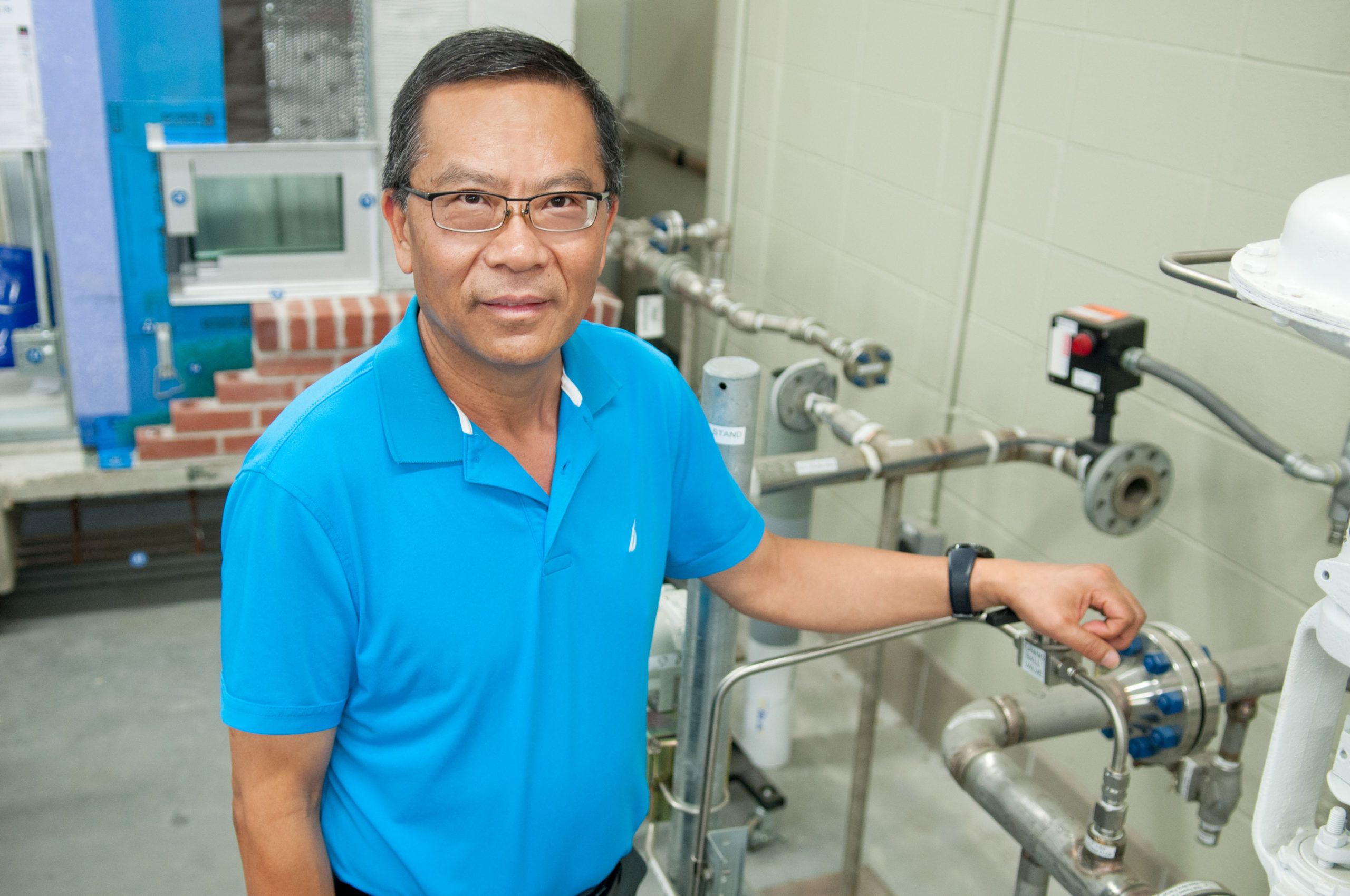
Construction catches up
Industrial contractors, often late to the game in adopting new technology, are also testing the digitization waters. In July, the Construction Industry Institute began researching a new platform dubbed Operating System 2.0 near its headquarters at the University of Texas in Austin.
The OS 2.0 platform will also promote standardization, digitization and automation, and support a greater reliance upon off-site modular construction in a manufacturing setting, all of which will reduce drags on productivity. Also to be addressed—blockchain and smart contract technologies that could more efficiently manage transactions and encourage a more timely payment process.
Ultimately, they hope to achieve a 35% reduction in project cost, 50% reduction in schedule duration, and 60% improvement in ROI. As direct beneficiaries, ExxonMobil, Shell, Canada-based Suncor Energy, Australia’s BHP and Saudi Arabia-based Sabic have contributed $2 million in support of the research.
John Fish, director of project support services at design firm Ford, Bacon & Davis in Baton Rouge, was an early proponent of the effort. Fish serves on CII’s board of advisors and assists with research and technology, and says the OS 2.0 concept has been a long time coming.
He says the name of the platform denotes a desire to take the construction industry to the next level. “Over the last 50 years, the construction industry has not had any significant productivity gains at all, while manufacturing has improved by some 200 percent,” Fish says. “We’re just coasting along, doing business like we always have. Some argue that we have even become less productive.”
A consortium of investment partners launched a private entity—PrairieDog Venture Partners—to actualize and deploy OS 2.0, even as research is getting under way at UT’s Cockrell School of Engineering. The standalone company is financed by the Construction Users Roundtable (CURT), along with other private shareholders.
In 2020, PrairieDog hopes to deploy a “minimally viable product” to be used in various pilot projects. The product can then be augmented as new research is completed. “The research and development go hand in hand,” says Peter Dumont, executive advisor at Premier Resources Group in Houston and one of the principal investors in the platform. “We’ve got the research at UT and the PrairieDog business to test these research concepts as they come out of the laboratory.”
Dumont is currently scouting for contractors and industrial owners interested in supporting the pilots. He’s also in negotiations with a Baton Rouge-area technology company that could play an integral role in the platform’s deployment.