It all began years ago, when industrial owners started digitizing their processes to gain more operational insight into their facilities. Whether they knew it or not, they were laying the groundwork for what would one day give rise to a host of emerging technologies once considered impractical.
In the early years of the annual Tec-Next Conference at Baton Rouge’s Shaw Center, ideas such as digital twins, generative AI, robotic inspections and virtual reality-based training were being tossed around, but they seemed more academic than practical in the industrial space.
That’s all changed now, and tech experts warn that if industrial owners don’t get on board they’ll risk being left behind. In many ways, the industrial market was late to the game, says Eric Allen, CEO & founder of San Francisco-based Environmental Intellect (Ei). “I graduated in mechanical engineering just as the iPhone launched, and Google Maps would help get me to the refineries,” he adds. “But once I got to the sites, I’d have to leave my phone in the car and use paper maps.
“That got me wondering, why wouldn’t a high-risk environment such as a refinery have the best in technology? It was then that I began looking for better ways to serve our customers.”
At the time, his then-fledgling company was digitizing CAD drawings for industrial clients. Then, in 2016, Allen’s workload quickly accelerated as his customers began looking for ways to utilize 3D scans of their facilities. “We began developing a way to view our customer’s existing data in a web browser,” he says. “It became a platform for delivering and using digital information.”
Today, many of Allen’s clients are situated along the I-10/I-12 corridor, where he builds tools for industrial facilities between New Orleans and Baton Rouge. Ei employees first identify the problem and determine how far along a customer is in their digitalization journey before proposing a solution.
“We’re big on usability,” Allen says. “The technology must be packaged in a way where people can actually use it. We’ve learned you can’t be too ahead of your users. We take more of a targeted approach in solving problems.”
The world is changing, he says, and industrial owners need to change, too. “People in maintenance, operations or heavy engineering are saying it’s hard to find people because they don’t want to show up at the plant every day and use old legacy tools,” he adds. “They’d rather go work at Amazon or some other tech company. When a company is behind in technology adoption, it makes it harder to recruit people.”
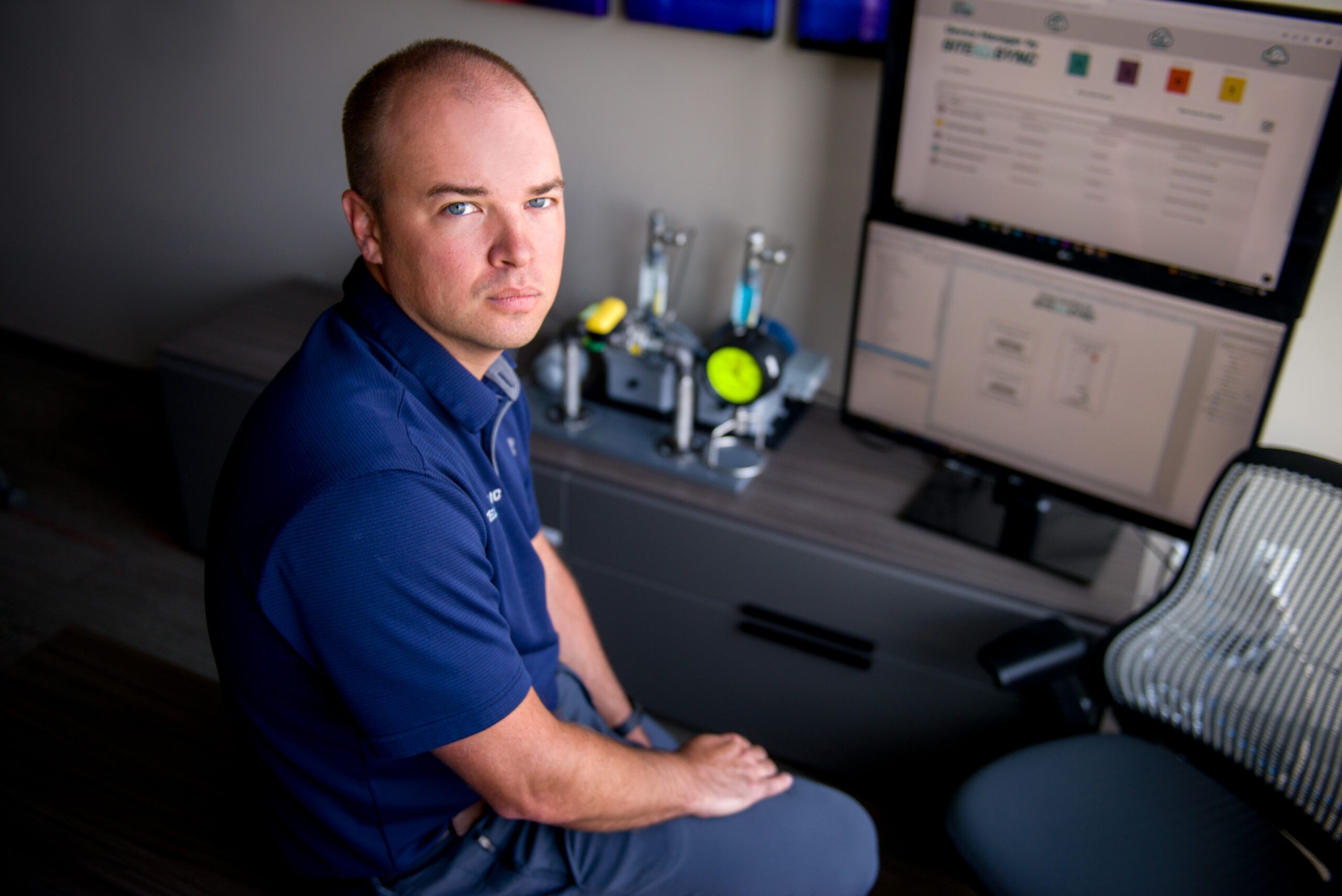
Tools of the Trade
Today, Allen’s company markets its proprietary digital twin tool, which his customers use for everything from maintenance to capital projects to operations. “Some are using it to commission units after a turnaround,” he says, “while others use it for training so they can understand the unit without going out in the field.”
AI is a key component of the tool. For example, one of Allen’s south Louisiana customers has deployed machine learning technology to identify vessels and track greenhouse gas emissions.
“We went into some of these facilities and scanned them for a couple of days, then trained the algorithm to find leak points in the model,” he adds. “Something that usually takes months we did it in a couple of weeks in the field.”
They’ve also begun to assist some plants with studying the implementation of ChatGPT or generative AI to identify and prioritize potential uses. “Large Language Models (LLMs) can do a good job of mining key information out of a large amount of legacy documents,” Allen says. “There are a lot of opportunities for ChatGPT in that space.”
Michael Brauer, vice president of operations at BBP Sales in Baton Rouge, is excited about the potential of emerging tech, especially now that many industrial plants’ data connectivity issues are being resolved.
BBP has taken a deep dive into the wireless and IIOT (Industrial Internet of Things) side of the tech world, helping customers connect wireless sensors to their existing systems and providing other end-to-end solutions.
“We have a ton of IIOT and OT knowledge up and down the river from Baton Rouge to New Orleans to leverage,” Brauer says. “It’s one of the best places in the nation to take advantage of some of this technology.”
Today, plants have digital transformation teams that seek better insight into their processes, while also reducing the labor hours needed for logistics, predictive maintenance and reliability functions.
“In the past, it would’ve cost tens of thousands of dollars to deploy vibration monitoring,” he adds. “Now, they can deploy low-cost OT sensors to provide baseline data to let them know which asset they should monitor. It’s making existing assets and investments smarter and helping people make sense of large amounts of data.
“And with data in a central place and standardized in the same way, AI algorithms can help automate the insights that a company is looking for.”
Bauer says some of the new AI technologies, such as ChatGPT, have potential in the industrial space, but warns that owners should be cautious.
“I would never put my customer’s data into ChatGPT because a lot of that could get published into a public model. We take security very seriously here,” he says.
“Although we do see its value in the automation of repetitive tasks … such as when you have code in one programming language and need to change it over to another project. That’s huge in an industrial environment because programming time is hard to come by.”
ChatGPT can also index and provide access to information faster than other search engines.
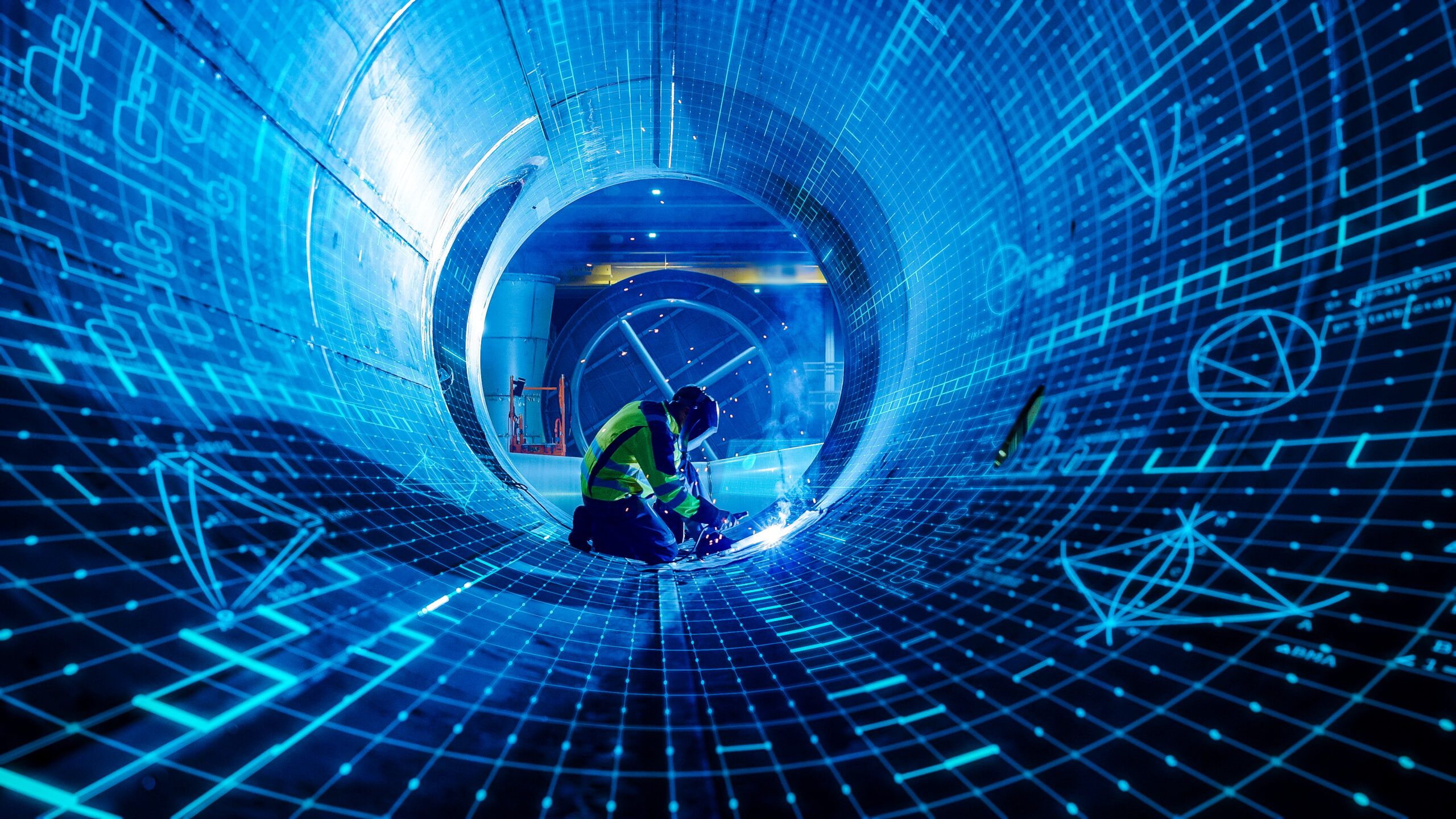
It’s Getting Real
Some of Louisiana’s larger petrochemical complexes have become true trailblazers in the tech arena by going beyond mere beta tests to the full implementation of technology into their processes.
Coila LaFleur, enterprise architect at ExxonMobil Baton Rouge, is tasked with finding ways for technology to support various businesses strategies at her facility. Given the size of the Baton Rouge complex, “we’re a great playground for new solutions,” LaFleur says. They’re currently using a pipe inspection robot—developed by a third party—that crawls autonomously along a length of pipe to perform inspections. Other ExxonMobil facilities even use robotic dogs to make rounds and take laser scans of the facility. “You can attach so many different things to a robot to enable it to detect gas leaks or go into some other dangerous situation where you don’t want to send a human,” she says.
LaFleur says the Baton Rouge complex is currently “on a journey” to implement digital twin technology. “One of the big challenges is how do we take all of our 3D scans, all of those data-driven models, and bring it to a place where people can get to it?” Their hope is to create a central repository for the 3D data, then develop an industry data standard that will allow them to collaborate and share data with other companies. “Using that same data standard will allow us to do that seamlessly,” she adds.
Only then will ExxonMobil be able to move fully into the digital twin world, “where we will have a full-scale model of the facility with real-time data flowing through it. That’s when we’ll be able to see a particular pump, for example, and the current pressure on that pump. We’re not there yet, but we are on that journey.”
ExxonMobil also has AI experts in offices in Houston and Argentina that are researching practical ways to implement LLMs such as ChatGPT.
“We’re trying to figure out how to use them to our advantage,” LaFleur says. “And then, of course, there are concerns around cybersecurity, so we’re trying to figure out what’s the best technology to use that will provide more functionality, as well as be secure.”
A technology trailblazer in its own right, Shell has made noteworthy advances in the implementation of digital twins.
David Mustain, Shell’s digitalization and innovation lead in Geismar, says it all began during a Tex-Next Conference a few years ago. “Someone asked, ‘Who will be the first to build a functional digital twin and keep it up to date?’ We took that as a challenge and began making local investments to move in that direction.”
Shell’s Geismar plant has now implemented a digital twin and can “walk” through some of its units using virtual reality.
“Our project designers, maintenance engineers and support inspectors can all go to one spot to search for a tag, then find the associated process drawing and specs related to it,” Mustain says. “They can fly to that spot in a 3D model or pull up point cloud information and see a 3D visual of the area. We are still at the early phases, but we are already seeing significant gains in our ability to avoid trips to the field and maximize efficiency of maintenance planning.”
Globally, Shell has also had success using remotely controlled ground robotics, and the Geismar site has used a robotic pipe crawler for inspections. AI also has significant potential, Mustain says. The Geismar site is utilizing multiple AI models developed by other Shell sites and co-developed with Baker Hughes and Bentley Nevada.
Additionally, Shell’s partnership with technology provider C3.ai enables it to deploy enterprise AI solutions at scale.
“AI and ChatGPT get a lot of focus these days but there are other subsets of AI, such as machine learning, that have real current potential,” he adds. “Our global team developed a predictive machine learning model to track the performance of equipment. We took that and used it to track performance of control valves and other equipment.
“These tools can give us early indications that something is changing. We can then make corrections without disturbing the plant or requiring a shutdown. The model is actually teaching itself what normal looks like. We turn the model on and let it track the equipment over time.”
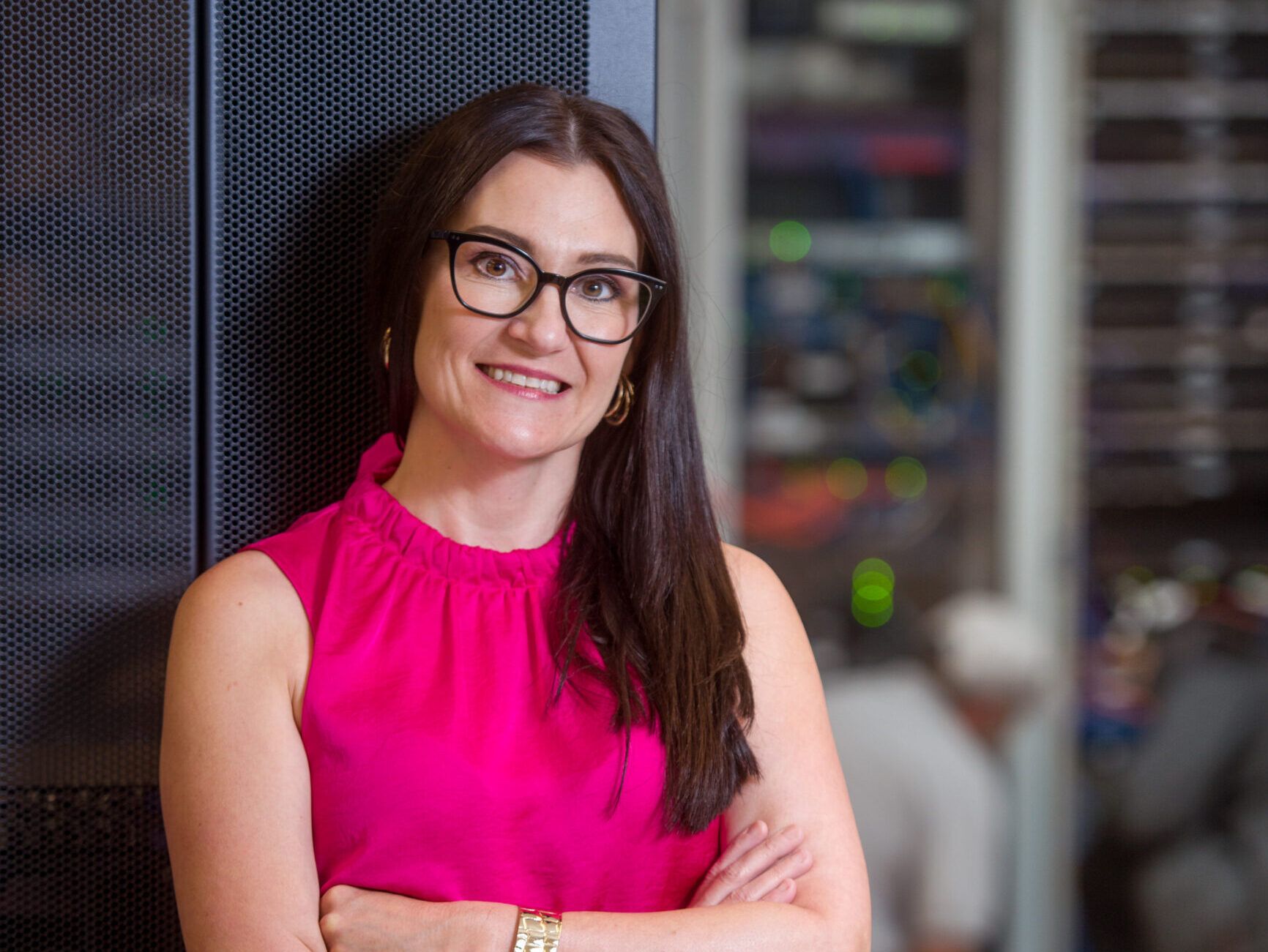
Envisioning an AI Future
Equipping both workers and managers to implement and utilize emerging technologies will be the next big challenge for industry, particularly given the speed in which these technologies are evolving.
In that respect, Andrew Schwarz, a professor in LSU’s E. J. Ourso College of Business, is ahead of the game. Some five years ago, Schwarz envisioned that AI would become immensely important in the corporate world.
That’s when he spearheaded a new “Emerging Technologies” specialization in the school’s Executive MBA program and included a course in AI strategy as part of the curriculum. The coursework also focuses on cloud computing, cybersecurity, policies, programs and governance.
In his MBA class, Schwarz focuses less on the technical components and more on “making the business case” for AI. He has students complete an applied project where they incorporate AI into their own organizations. They then talk about how they would go through a transformation to achieve their objectives.
Most of those in his class are executive MBA students and online executives, many coming from the petrochemical space.
“The class requires them to understand the tech and the organizational challenges associated with it,” he adds. “It’s more about building resiliency in your organization. There’s a misconception that AI will automate processes and therefore be used to cut jobs. But if you’re using tech to cut jobs, you will be disappointed. You’re merely repurposing your workers to higher level positions. It’s making your workforce more competitive by allowing them to focus on the insights that matter.”
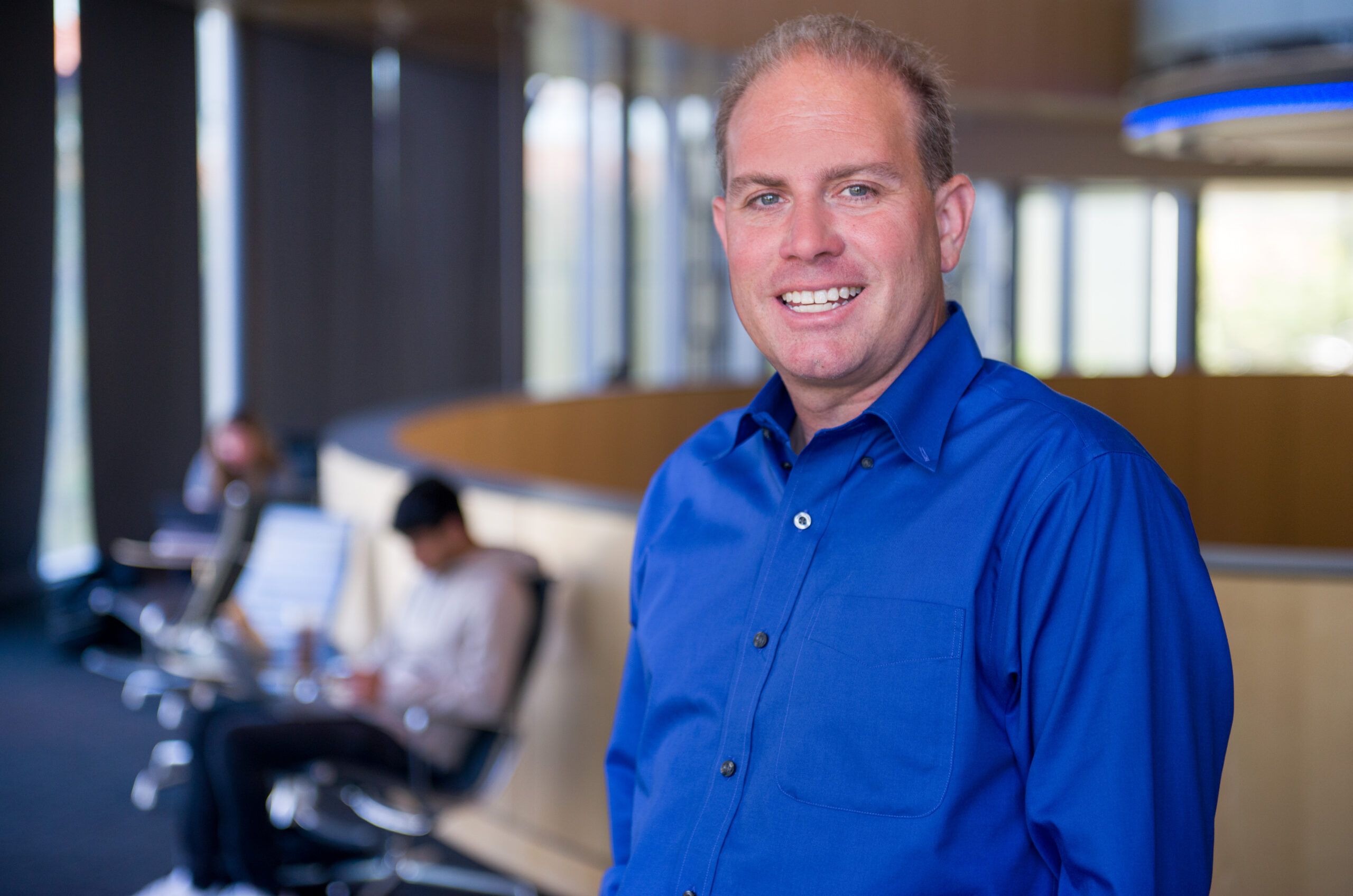
Nevertheless, determining what objectives can be accomplished with AI is not an easy task for industrial owners.
“You have to figure out if you’re using AI to grow your business, smooth your processes or if there’s some other underlying driver,” he adds.
“You must start with the business case first. Once you start to unpack that, you start to identify sources of data and figure out where the data will need to come from to meet those objectives. That’s the beginning of adopting AI. The mechanisms and modeling are a whole different category of decisions.”
Schwarz predicts that AI will ultimately be integrated into all organizations, and that manufacturing and the industrial market will be revolutionized in the process. “But you don’t have to go all in,” he adds. “You can start small and learn, then expand based upon what’s good for your organization. The more you get into it, the more you’ll realize its potential.”
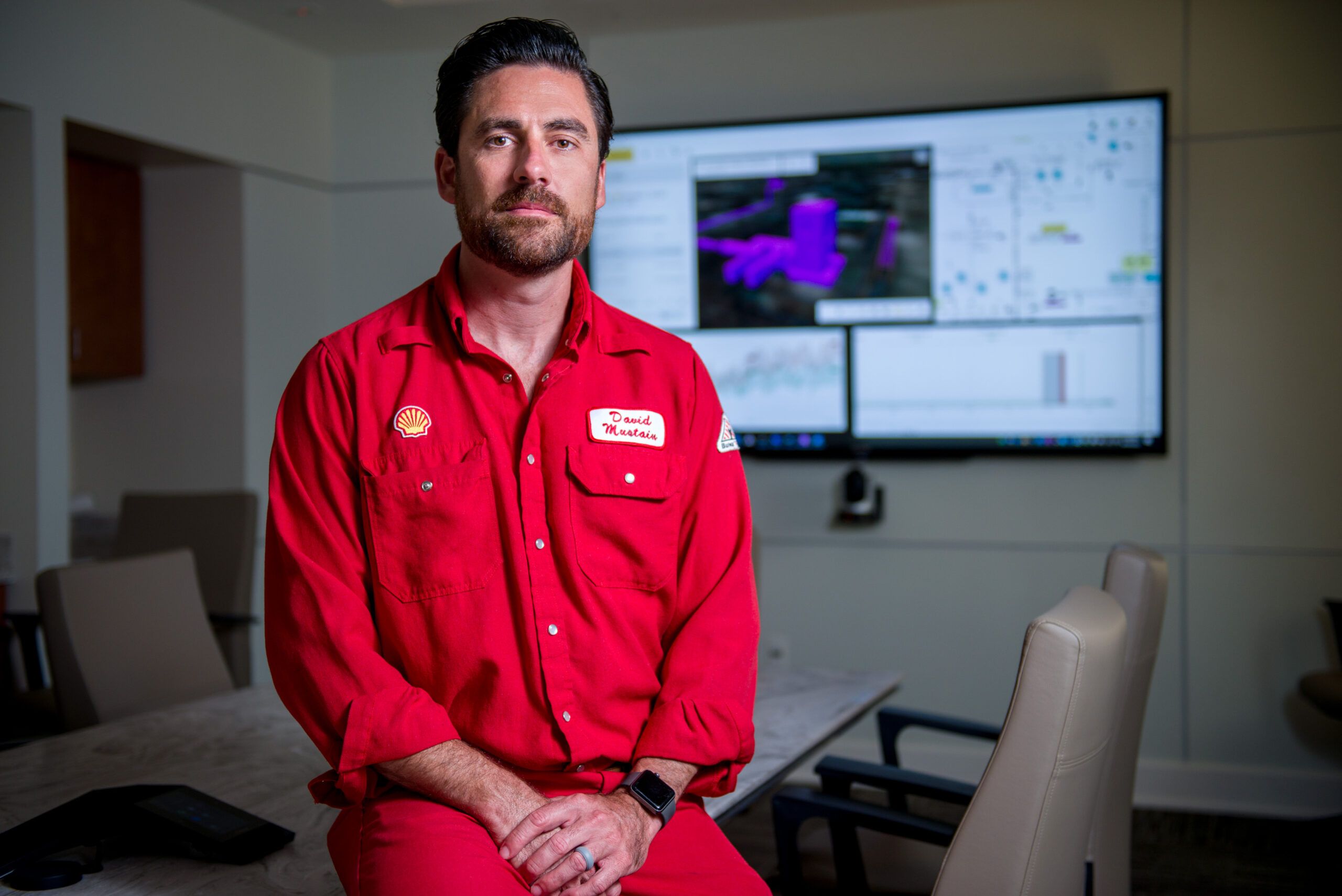
Overcoming Resistance
New technologies are great but mean nothing if companies can’t get “buy in” from those using them, says ExxonMobil’s LaFleur.
“If your users don’t understand the benefits of the new technology, then you’re not going to get any value out of it,” she says. “Adoption is something that we heavily focus on at ExxonMobil, and I think we’re doing a good job at that.”
ExxonMobil assigns a change management advisor to every IT-related initiative, who in turn works closely with the end users to ensure that the change is fully implemented. In the process, they seek to show them how the technology will make their lives more productive, as well as generate value for the company.
Additionally, they support workers through the transition process by providing the training or tools that they’ll need. Equally critical, they incorporate the new technology into the onboarding process for new hires.
“If you don’t get people ready to change the way they work, then the technology won’t be integrated into their daily processes,” LaFleur says. “We have multiple examples of good solutions that were developed, but we didn’t target the change in the right way, so they never got used.”
Shell’s Mustain says there are other obstacles to overcome, including a sometimes-steep technical learning curve and a certain amount of financial risk should the technology be deployed too soon or unnecessarily.
“Is it more important to be the first to apply the technology or more important to guarantee long term success? Then there’s a change management side of it … are we willing to change our behaviors and trust the technology?”
Henry Hays, co-founder of DisruptREADY in Baton Rouge, agrees that implementing technology for the sake of technology can be counterproductive. “But companies shouldn’t sit on the sidelines either,” Hays says.
“We always tell people that AI won’t take your job; someone who knows how to use AI will take your job. People with a positive mindset on this change will probably win.”
DisruptREADY is a strategic advisory firm that helps executive teams keep up with the rapidly evolving world of technology.
“New technologies will come at you fast so you need to have the ability—under roof—to assess and figure out what to do with it, as well as help decide if you should start using it,” he adds.
“If you spin it the right way, the young folks will come looking for you as opposed to other businesses. The time is now to step into this. Kodak should’ve been Instagram today, but they decided to keep selling camera film. And Blockbuster waited on the sidelines as its industry evolved and now they’re no longer in business. They did not see the warning signs.”
ExxonMobil’s LaFleur is excited about a future where new technologies will transform the industrial workspace. However, some owners are failing to realize its full potential.
“We’re underutilizing things such as AI and robotics,” she adds. “I talk with my industry counterparts a lot about that. These technologies are going to change the way people work in a good way. Humans will be able to do what they do best, and these new technologies will handle all the mundane, repetitive and dangerous tasks. That’s what gets me up in the morning.”