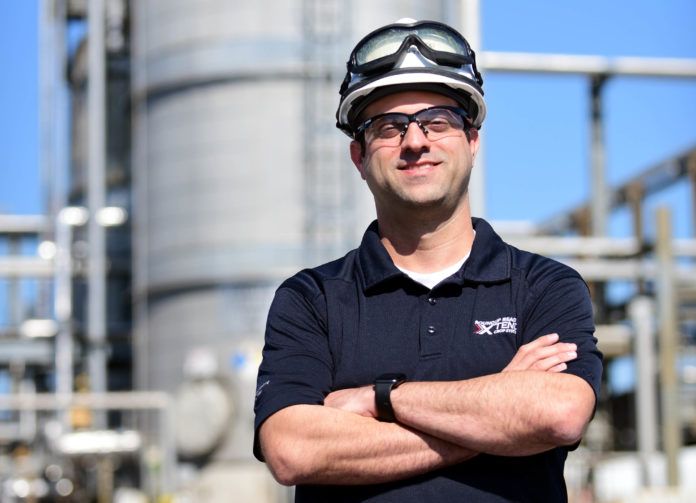
Time is money, and that’s entirely too evident in the world of industrial maintenance. Planned turnarounds at Gulf Coast plants account for a mere 25% of maintenance downtime, with the remainder coming from unplanned breakdowns, outages and shutdowns.
While planned turnarounds directly impact an owner’s bottom line, the real financial danger comes from unexpected events. That’s why industry has begun to turn its collective eye to a “predictive maintenance” strategy in the last five years, as it seeks to transform maintenance from a time-based process to one based on need.
Predictive maintenance incorporates predictive analytics and machine-learning algorithms based on historical and real-time data to identify specific issues. In addition to helping prevent downtime, a predictive maintenance approach can better identify true maintenance needs and can be useful in industries where the uptime of critical assets drives the bottom line.
In Luling, Bayer Crop Science hopes to become an industry leader in this regard, as it integrates three key components of predictive maintenance during its current $975 million fertilizer plant expansion, to be completed later this year. Formerly owned by Monsanto, the plant hopes to change the way equipment health data is integrated into its business systems for better decision-making and increased asset availability.
Bayer believes it can use the new production facility as a means to develop better systems for reduced downtime across all its plants. In the process, it hopes to increase equipment availability, reduce staff exposure to hazardous locations and reduce the risk of cross-contamination with the existing facility.
Derek Taravella, the maintenance and reliability systems technology specialist for Bayer Crop Science, is working to support integration activities on a global scale, developing a new “one company strategy” for maintenance and reliability systems.