LM Wind Power had already forged several crucial alliances by the time it unveiled its new Technology Center for the Americas in New Orleans last November. After all, the international wind turbine manufacturer would eventually need 100 direct and 220 indirect workers to support the facility, in addition to a voluminous 60,000 square feet of manufacturing space at NASA’s sprawling Michoud Assembly Facility.
Still in the early stages of the journey, the TCA facility will ultimately test a variety of new techniques for designing and building wind turbine blades, and support four of LM Wind Power’s largest facilities in Brazil; Canada; Little Rock, Arkansas; and Grand Forks, North Dakota.
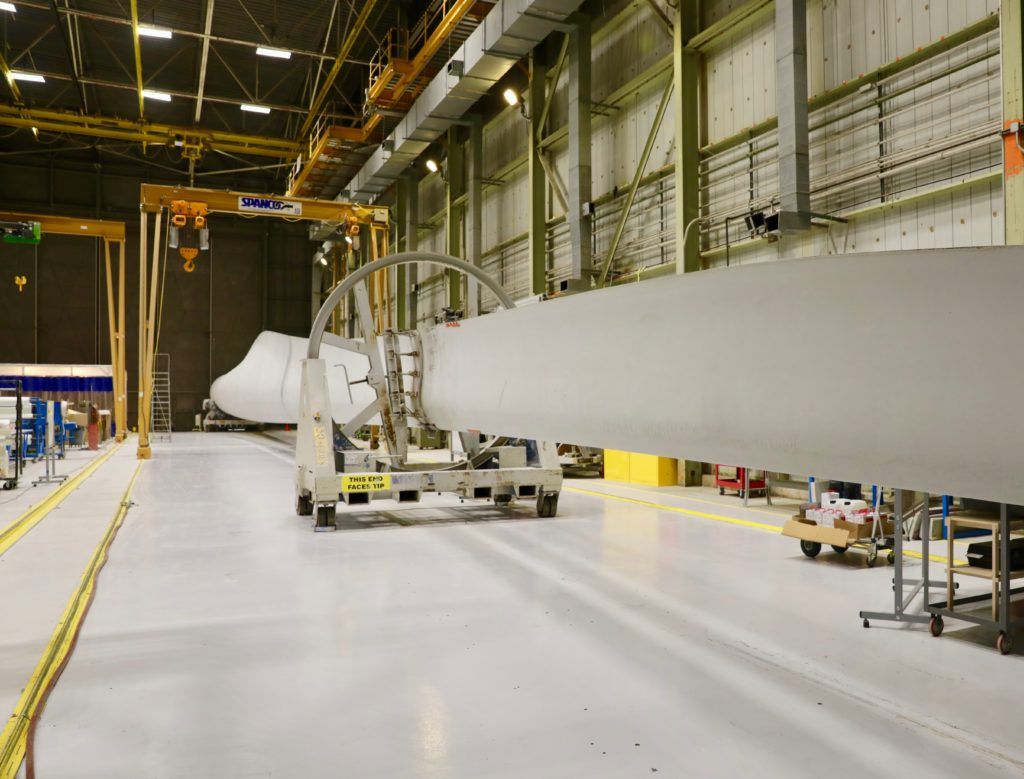
TCA Director James Martin says the facility is intended to provide the Denmark-based company with a local presence for its North American customers, adding that the New Orleans site is well-situated to serve the rapidly growing wind power market in the U.S. “This will establish a technical and a customer support footprint, and New Orleans and Louisiana have the best value proposition to support the region and our customers,” Martin says.
Once fully operational, the TCA facility will field a diverse team of physicists, engineers, draftspersons and composite technicians, among others. “One of the special things about TCA is that you have manufacturing and design working right next to each other,” Martin says.
Such cross-functional teams are vitally important for driving innovation, which will become increasingly important as the use of wind power becomes more widespread. There are more than 50,000 wind turbines in the field today, and all roads lead to substantial growth for both onshore and offshore applications.
At Michoud, TCA’s technology mission will be to drive down the cost of wind energy and make it more competitive with other forms of energy production. For example, recent work has sought to develop and enhance a jointed turbine blade, created as part of a collaborative project between LM Wind Power and GE Renewable Energy for its Cypress onshore turbine platform. The revolutionary two-piece blade design enables blades to be manufactured at longer lengths, while improving logistics and offering more siting options.
Martin says the longer blades can drive down the cost of electricity, and the proprietary design allows these larger turbines to be installed in locations that were previously inaccessible. “You can deliver the blade to the site in two pieces and join it together with a proprietary technology connection at the base of the tower,” he adds. “GE and LM Wind Power are the first in the wind energy sector to actually bring this to market.”
Read the full story in the latest edition of 10/12 Industry Report.